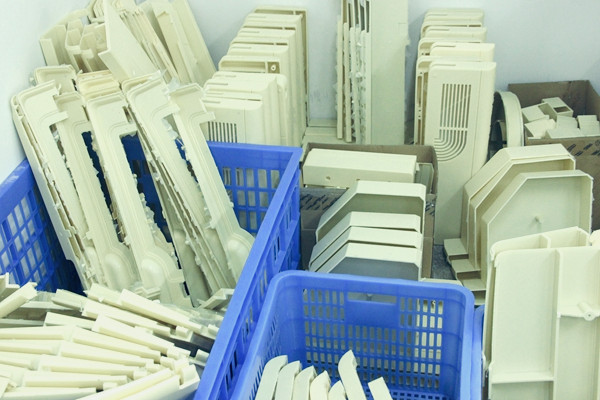
Thermoset Plastics Rapid Vacuum Casting
Vacuum casting Urethane is the best prototype and production way for the new product engineering test, concept proofing, market testing, Trial production checking, pre-production evaluation and low volume production. With 10 yeas experience in new product development and vacuum casting, Sanwo rapid Urethane Vacuum Casting for low volume production is on a lead of Vacuum Casting techniques in China, we offer a wide variety of branded materials for the urethane casting parts and we support the final product post finish service such as coloring, Matt, Glossy or Plating from start to the end, making sure that the Product from our vacuum casting process lead to a perfect final product.
Common Applications of Vacuum Casting
Urethane Vacuum casting parts no matter for small or big parts, hard plastic to soft rubber parts, or clear effect to opaque Pasts, Sanwo Rapid can accurately match all the design specification, product effect and consistent mechanical properties on accurate part replication. Common Applications of Vacuum casting are benefit from its material property and cost effective process.
1) Medical Device Shells Vacuum casting
Sanwo Rapid manufacturing company provides a complete set of rapid prototyping and manufacturing solutions for medical devices shells and enclosures. Among the many processes, Vacuum Casting is the best solution for the shells and enclosures copies from one prototype to low volume production in Urethane. Device parts from Hand grip model, rubber components, to Device shells and enclosures of Ultrasound machine, Ventilator, Carts, tables and panels, which the parts can be mold out as a single part without splitting and glued, and even over-mold with the waterproof Gasket, to ensure the strength, Function and assembly fitting for the Medical Device shells product.2) Car Lamps Over-molding
Most of the Car lamp prototypes are made by CNC machining as the PMMA material from CNC is as optical clear as the artworks. At Sanwo, we not only provide CNC machining for appearance Car Lamps and SLA Clear for form fit Car lamps, but also provide Clear Urethane Vacuum casting for low volume requirement, and provide Overmolding for the Car Lamps 2K molding requirement to make the clear lens and opaque lens housing as a single one piece. Either Opaque Housing overmold onto the CNC optical clear lens, or Opaque Housing over-mold onto the Vacuum casting clear Urethane lens, this Urethane Vacuum casting process is a perfect way for the functional and appearance models making.
What is a vacuum casting?
Vacuum casting, also known as urethane casting or silicone molding, is a manufacturing process used to create small to medium-sized batches of highly accurate and high-quality plastic parts or prototypes. Here's how it generally works:
Master Pattern Creation: A master pattern of the desired part is created using methods like 3D printing or CNC machining. This master pattern is typically made from materials like ABS plastic or other suitable materials.
Mold Making: A silicone mold is created around the master pattern. This mold captures all the details and features of the master pattern.
Vacuum Casting: The mold is then placed in a vacuum chamber, and liquid polyurethane resin is poured into the mold cavity. The vacuum helps to remove any air bubbles from the resin, ensuring a smooth and uniform casting.
Curing: The resin is left to cure and harden inside the mold. The curing time can vary depending on the specific resin used and the desired properties of the final part.
Demolding: Once the resin has fully cured, the mold is opened, and the newly cast part is removed. Any excess material is trimmed off, and the part may undergo additional finishing processes like painting, polishing, or assembly.
Vacuum casting is often used in industries such as automotive, aerospace, consumer electronics, and medical devices, where high-quality prototypes or low-volume production parts are required. It offers advantages such as relatively low cost for small production runs, fast turnaround times, and the ability to replicate intricate details and textures from the master pattern.
How accurate is vacuum casting?
Vacuum casting is generally quite accurate, offering high precision and fine detail reproduction. The process involves creating a silicone mold around a master pattern, typically produced using 3D printing or CNC machining.
Once the mold is created, it's placed in a vacuum chamber, and liquid resin is poured into the mold. The vacuum chamber helps remove any air bubbles from the resin, ensuring that the final cast is free of imperfections. This results in precise replicas of the master pattern with intricate details faithfully reproduced.
However, like any manufacturing process, the accuracy of vacuum casting can be influenced by various factors such as the quality of the master pattern, the properties of the resin used, the skill of the operator, and the condition of the equipment. With proper setup and execution, vacuum casting can achieve very high levels of accuracy and detail, making it a popular choice for producing prototypes, small-batch production runs, and parts with complex geometries.
Choose Vacuum Casting for Your Parts in Small Volume
What is the difference between centrifugal and vacuum casting?